Tradiční odvětví výroby skla hledá cesty, jak snížit uhlíkovou stopu. Sklářské firmy v Česku zvažují investice do nových technologií a řeší, kdo je v transformaci podrží.
Závod Barevka u severočeského Dubí vyrábí už od roku 1912 plochá vzorovaná skla. Typické pláty přímo z této výrobny tvoří skleněnou fasádu Památníku Tomáše Bati ve Zlíně, využívají se ale také v koupelnách nebo jako dělicí příčky v interiérech.
Původně se v Dubí vyráběla skla barevná, odtud také získal závod své jméno. Ruční výrobu nahradila postupně licí. Dnes tady pracuje přes 130 zaměstnanců.
Mezi zákazníky severočeské sklárny patří hlavně výrobci oken a dveří. Vyrobená skla se prodávají do Evropy, ale Barevka je vyváží také do severní Afriky a Jižní Ameriky. Denně se v nepřetržitém provozu vyrobí až 90 tun skla.
Na začátku února uvedli v Barevce do provozu unikátní linku Volta. Nadnárodní společnost AGC Glass Europe tady zkouší, jakými kroky by se mohla vydat dekarbonizace nejen evropské výroby plochého skla.
„Je to výzkumný projekt, závod Barevka běží dál jako obvykle. Máme své zákazníky a závazky. Aktuálně jsme ve zkušebním provozu, ale vše je postavené tak, aby se výroba nezastavila,“ popisuje ředitel dubského závodu Jiří Pilný.
Na projektu se AGC Glass Europe spojila s dalším velkým výrobcem plochého skla, francouzskou firmou Saint-Gobain. „Tady nejde o konkurenci, v otázce dekarbonizace je potřebná spolupráce,“ doplňuje ředitel.
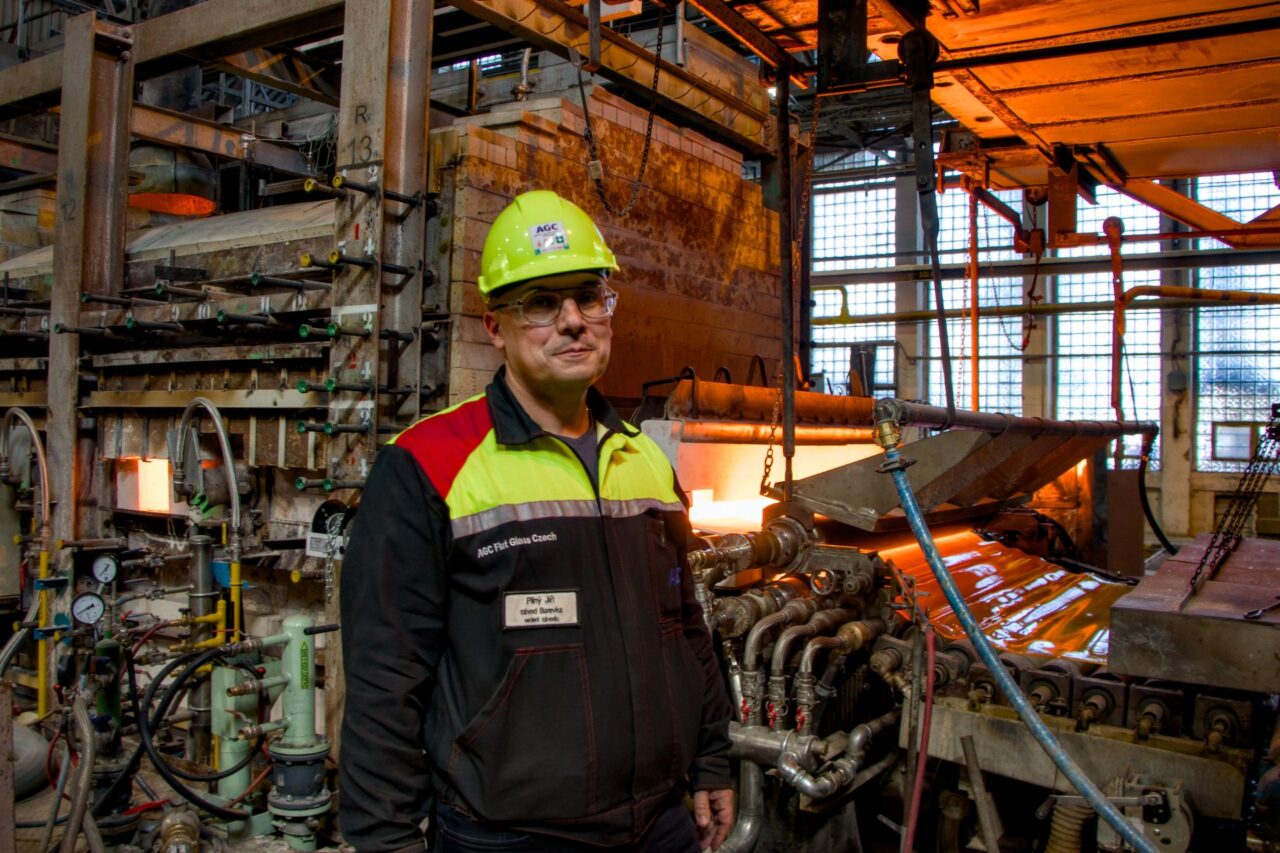
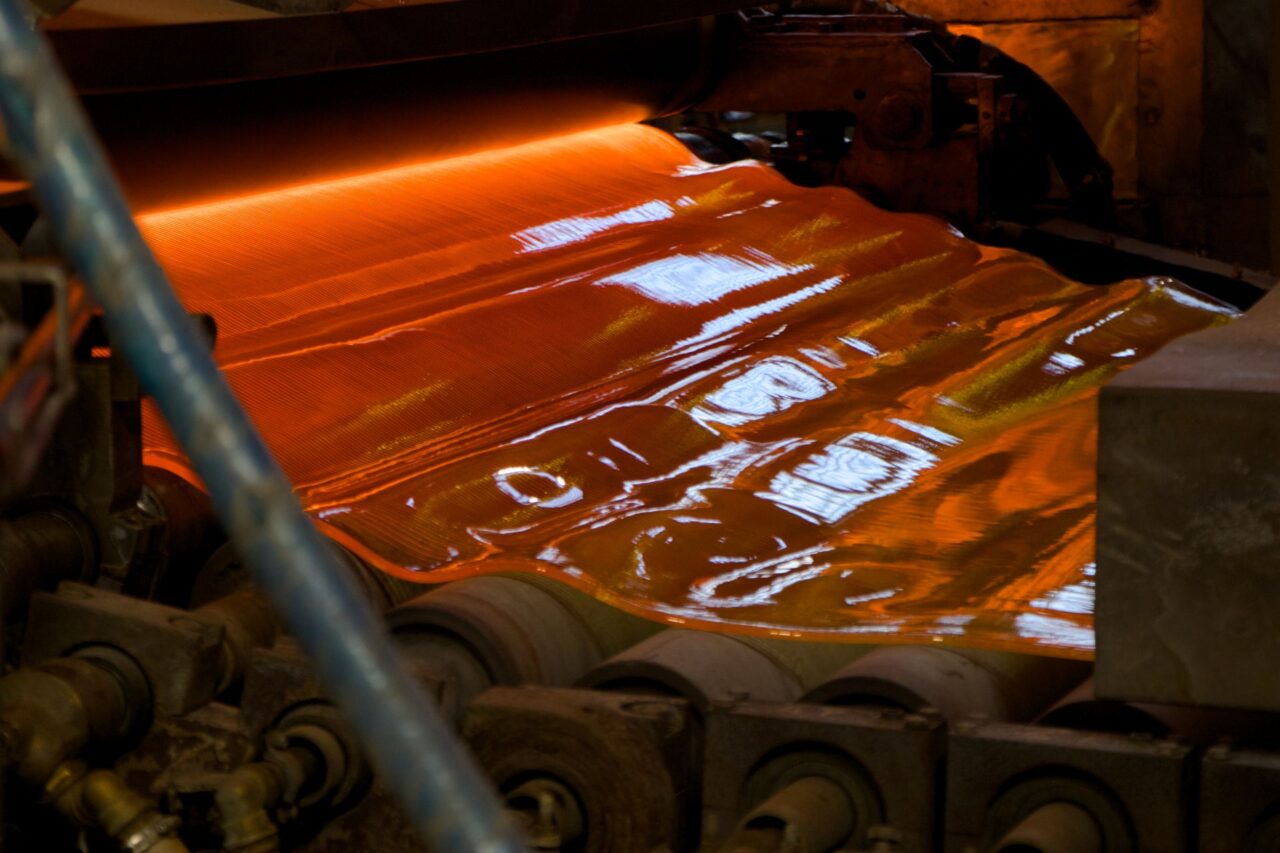
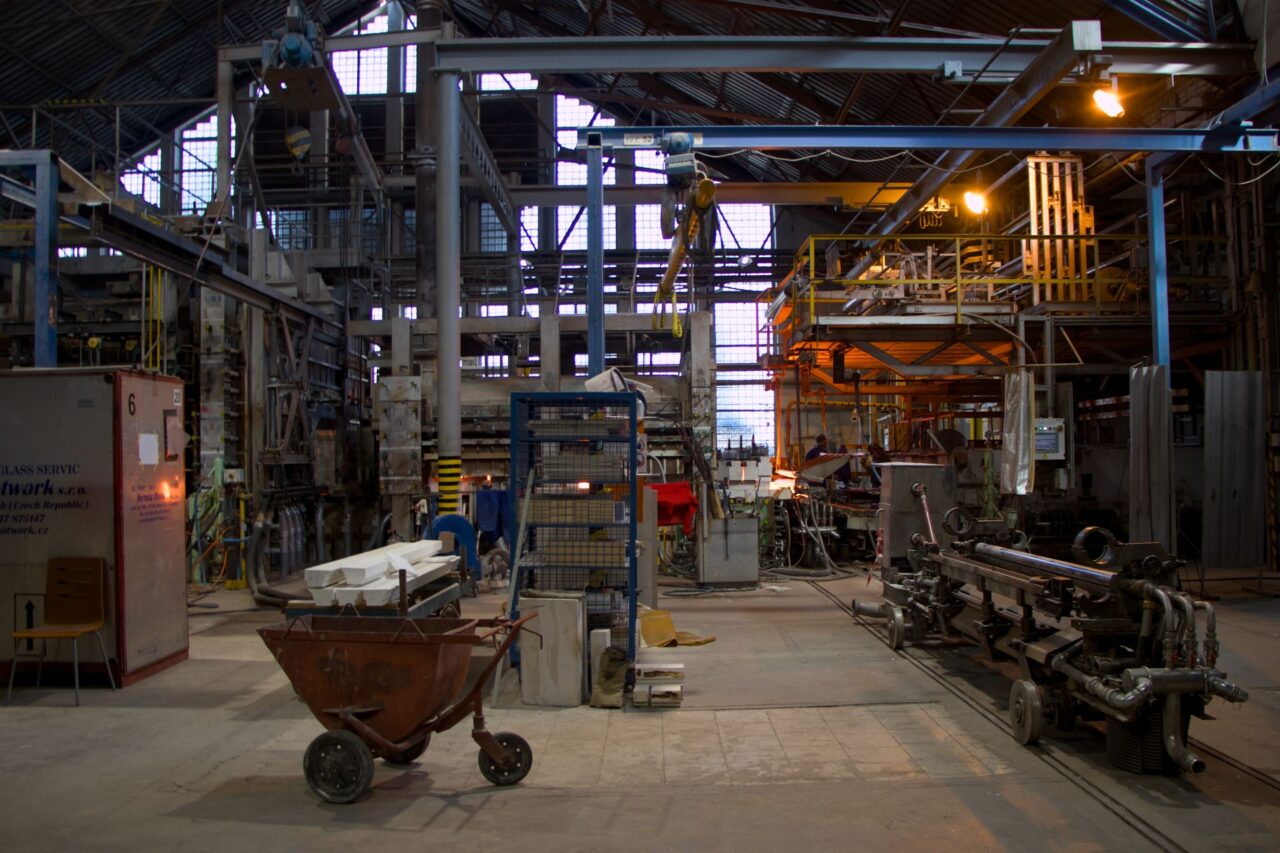
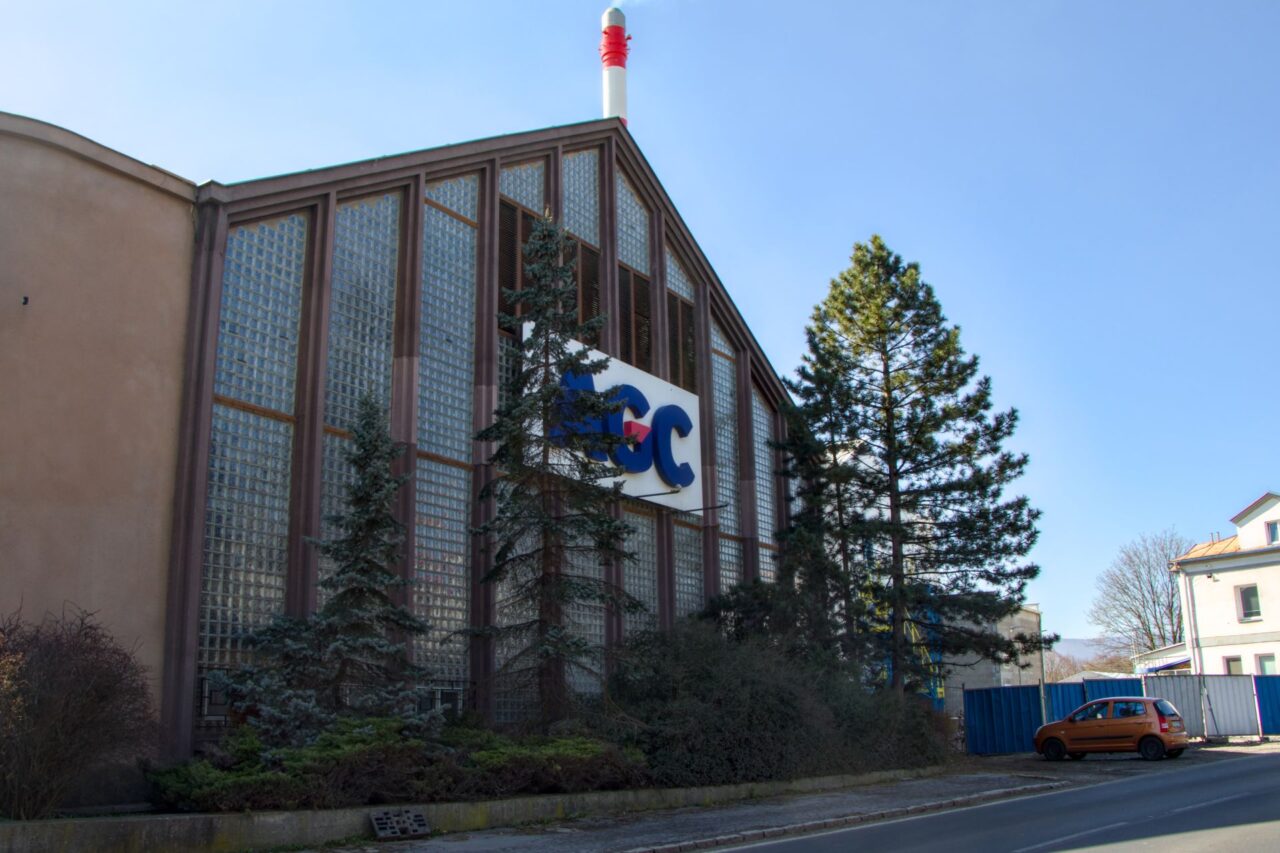
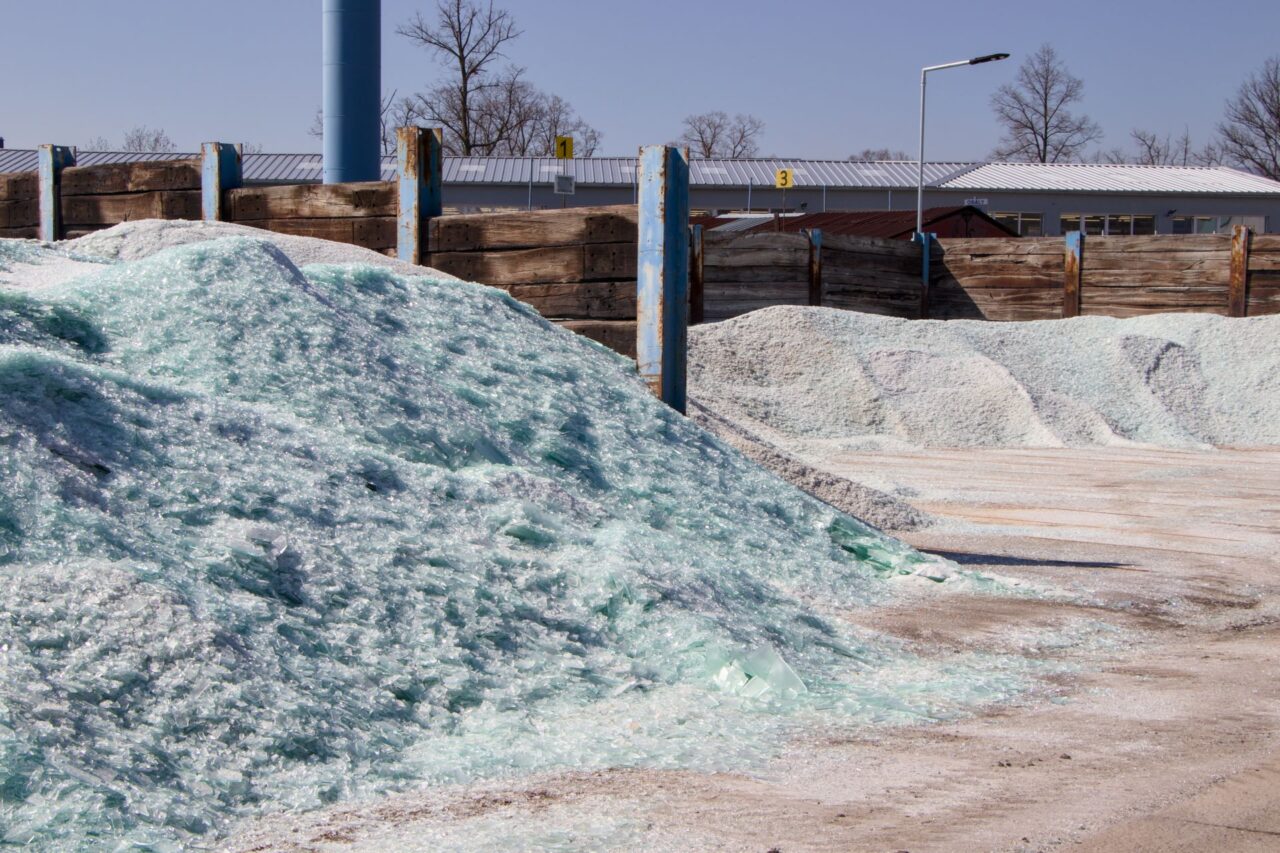
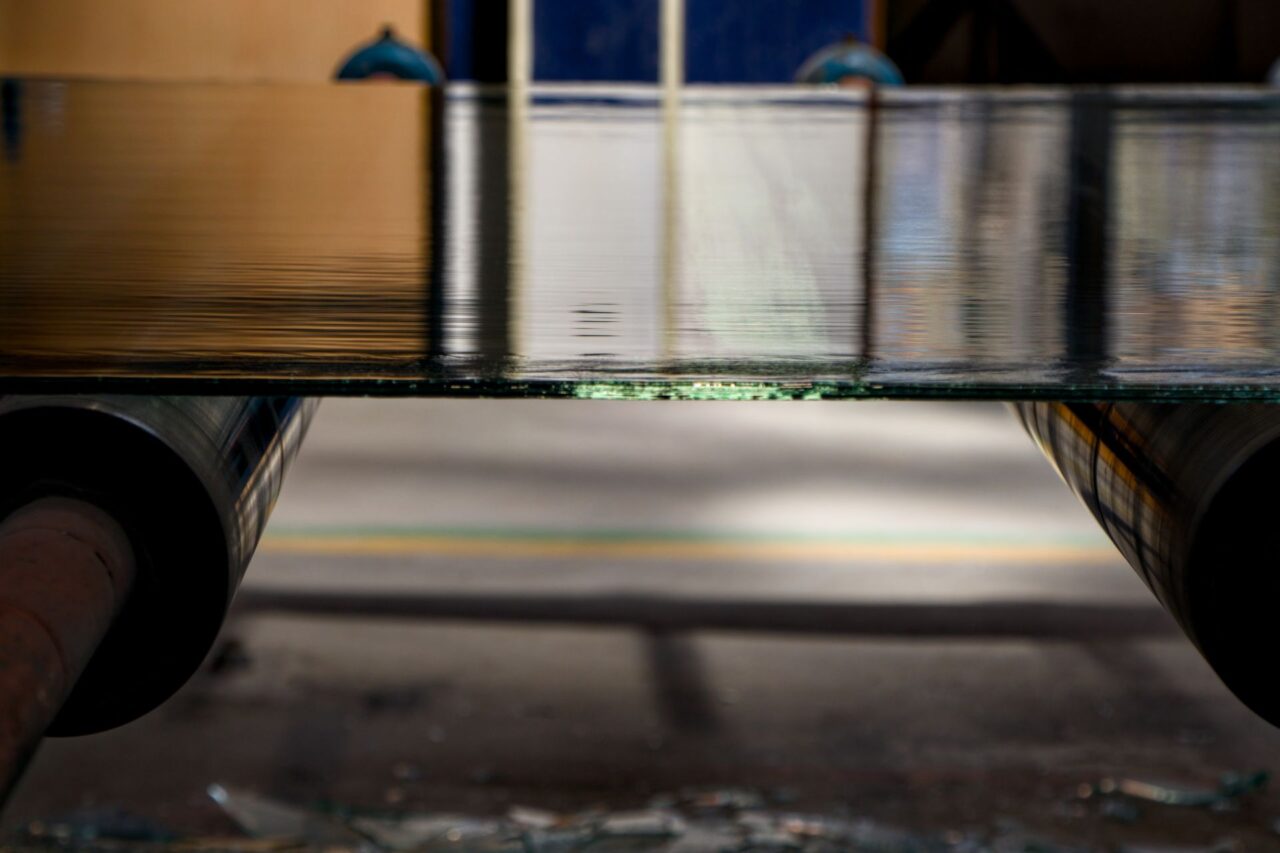
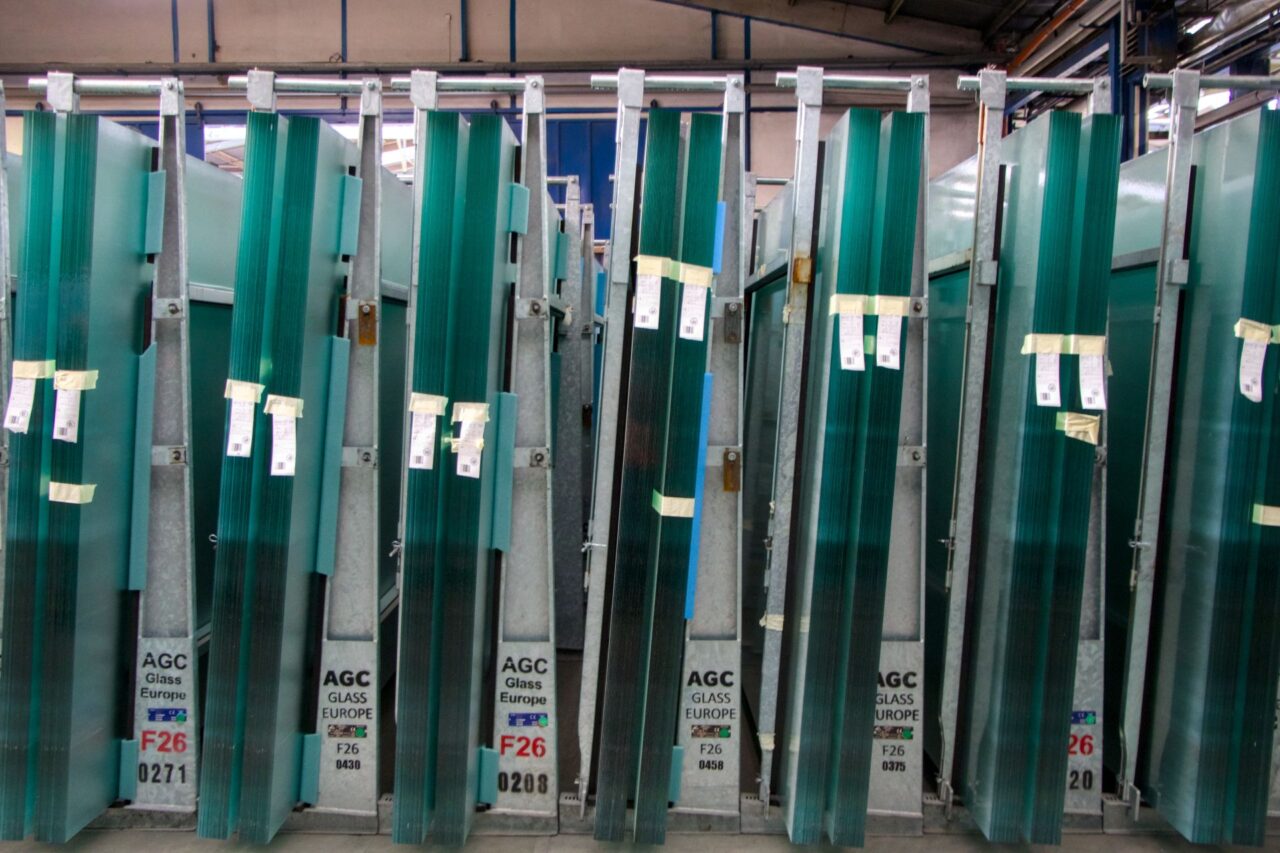
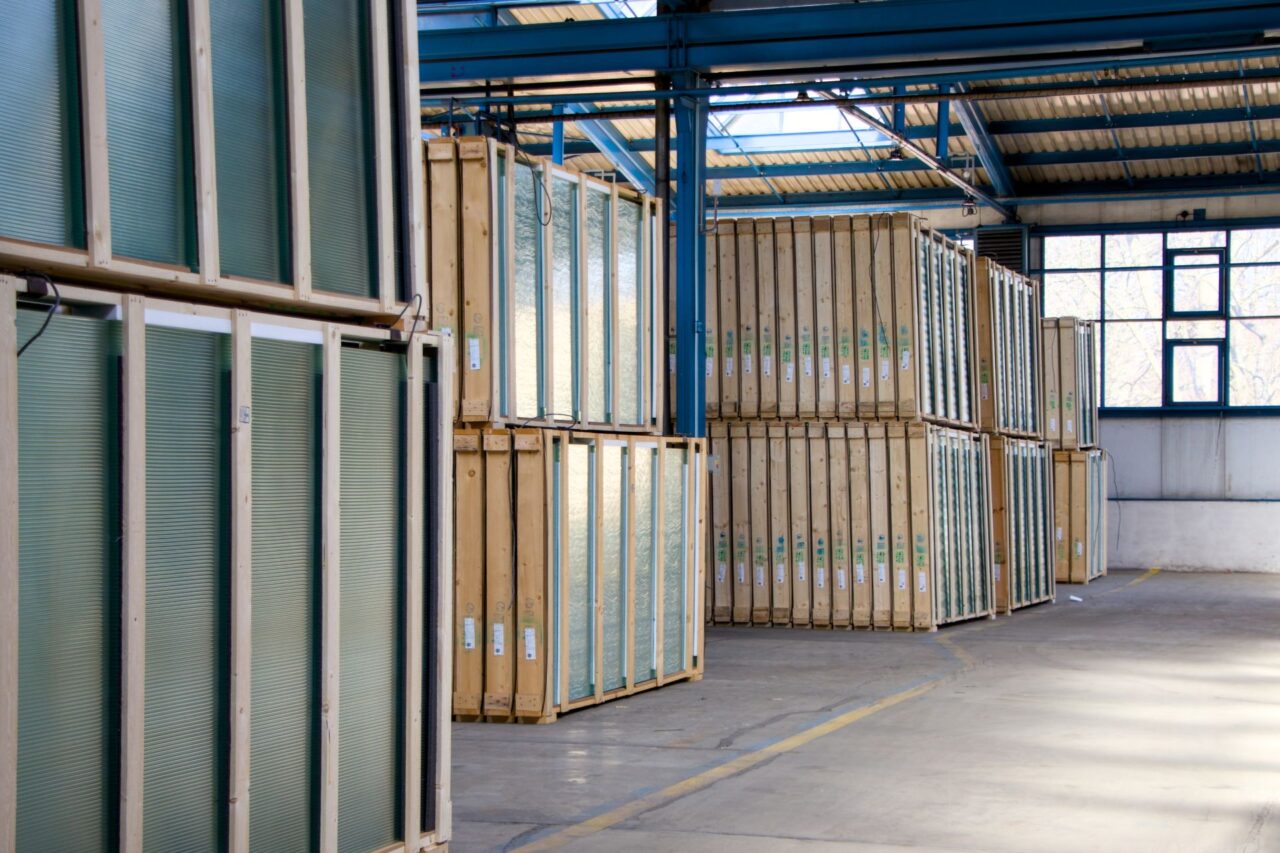
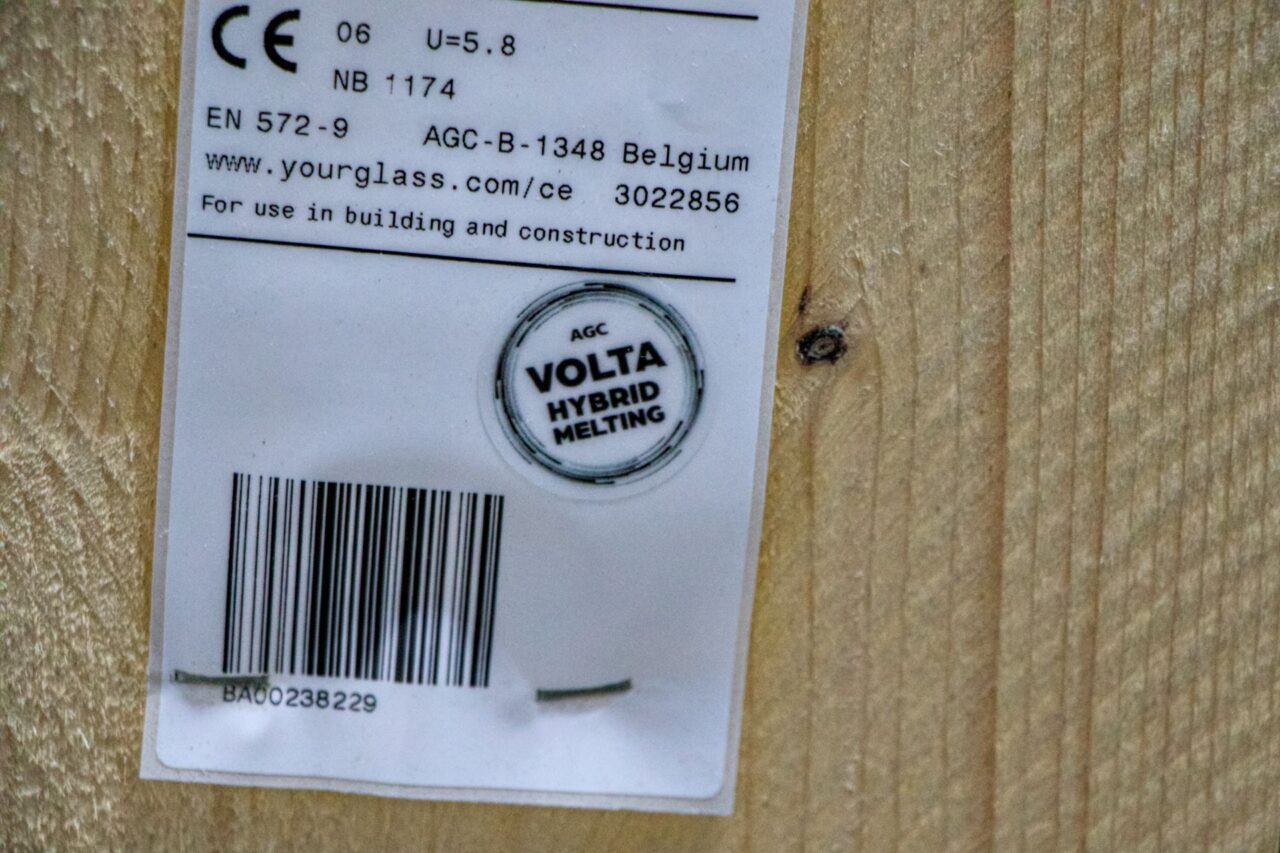
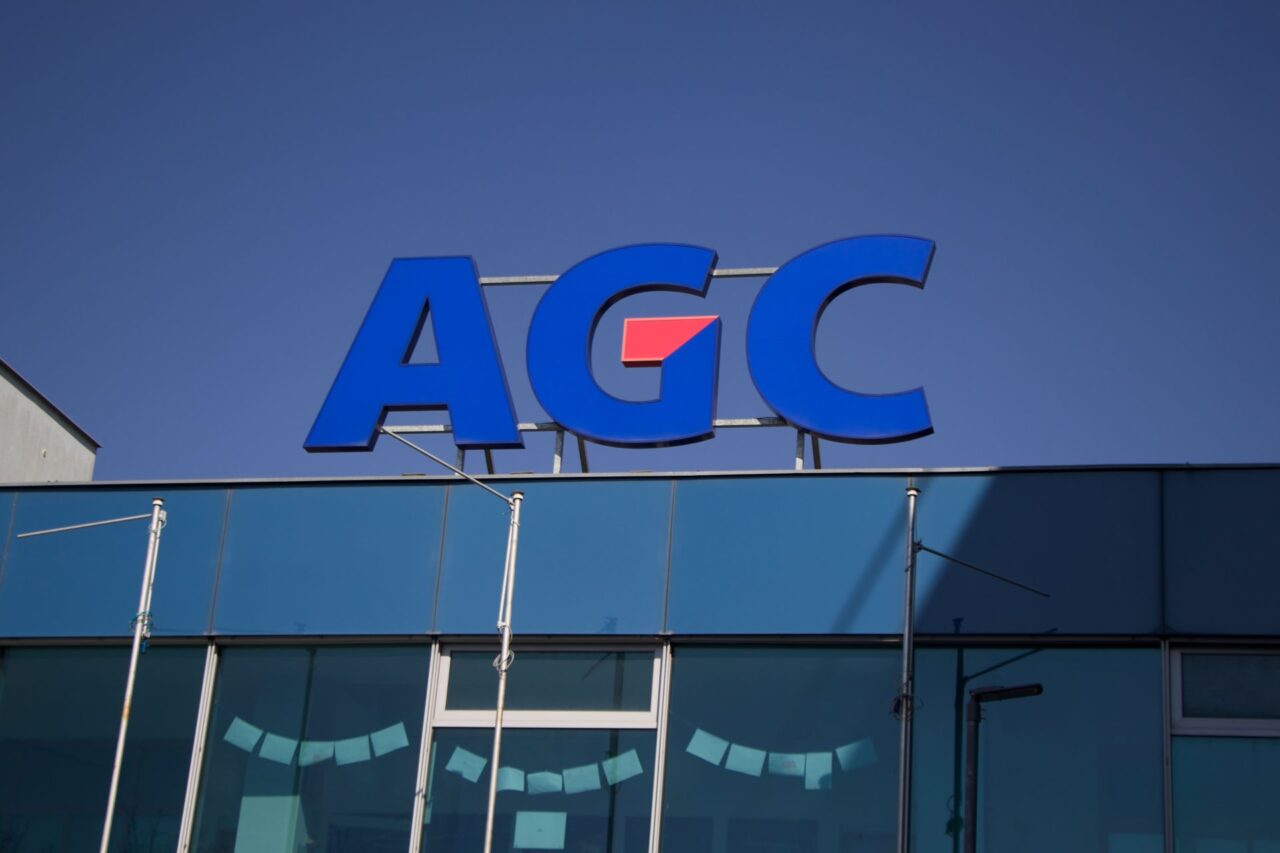
Testování Volty
Dosud tahle technologie bodovala jen v počítačových simulacích, nikde jinde na světě se při výrobě plochého skla nevyužívá. Její jedinečnost spočívá v tom, že se při tavení uplatní velké procento elektrické energie.
Jako palivo sklářům slouží obvykle zemní plyn. V hybridní tavicí peci se však z poloviny používá elektřina. Při výrobě se tak výrazně sníží spotřeba energie, protože tavení elektřinou je efektivnější.
Roli ve snížení emisí sehraje i využívání recyklovaného skla. Poměr střepů se bude postupně navyšovat až na 80 procent.
„Celá kombinace opatření přinese snížení emisí oxidu uhličitého o 70 procent,“ dodává ředitel Barevky. Nová pec „ušetří“ více než 193 tisíc tun ekvivalentu CO2 během prvních deseti let provozu. Celý sektor výroby plochého skla v Evropě má nicméně ročně na svědomí 4,6 milionu tun přímých emisí ekvivalentu CO2, z čehož tři čtvrtiny tvoří spalování zemního plynu.
Celková investice do linky přesáhla 30 milionů eur, tedy asi 750 milionů korun. Téměř polovinu částky, 300 milionů korun, pokryla dotace Evropské unie. Peníze putovaly z Inovačního fondu a mají podpořit konkurenceschopnost v energeticky náročném sektoru.
Technologii Volta teď čekají dva roky testování, zda bude využití vysokého podílu elektrického tavení pro velkovýrobu plochého skla vhodné. Na provoz dohlíží skupina výzkumníků a sleduje všechny parametry výsledného výrobku. Technologie z Barevky by se pak mohla případně používat i v dalších závodech společnosti AGC Glass Europe.
„Vana tady na Barevce má kapacitu 90 tun skla denně, další floatové linky ji mají až osmkrát větší. Naším cílem je ověřit si v menším závodě, zda se technologie dá využít například v Teplicích při výrobě plochého skla,“ doplňuje HR Country manager Libor Sehnal.
Dvě procenta emisí z výroby skla
Kroky k dekarbonizaci začali podnikat i další čeští skláři. Prudké zvýšení cen energií spojené s ruskou agresí na Ukrajině pro ně znamenalo velké finanční problémy. Celkově náklady v tomto období mohly stoupnout až pětinásobně.
Tržby odvětví se pohybovaly v roce 2023 podle Asociace sklářského a keramického průmyslu ČR okolo 58 miliard korun. Celkově v sektoru pracuje 17,5 tisíce Čechů. Mimo výrobu zmiňovaného plochého skla jde o obalové a užitkové sklo a skleněná vlákna.
Podle dat serveru Fakta o klimatu má české sklářství na svědomí dvě procenta tuzemského ročně vypuštěného ekvivalentu CO2. Hlavním zdrojem emisí je z 80 procent spalování paliva, většinou zemního plynu. Zbylých dvacet procent připadá na chemické reakce spojené se surovinami využívanými při výrobě.
AGC Glass Europe kromě vývoje elektrické hybridní technologie Volta využívá recyklované sklo a zabývá se celým dodavatelským řetězcem surovin. Zkouší také využívat jiná „zelená“ paliva, jako je biometan či vodík.
„Pro uhlíkovou neutralitu výroby plochého skla však bude nutné i nasazení technologií na zachytávání a využití, případně ukládání oxidu uhličitého, bez nichž nelze neutrality dosáhnout,“ vysvětluje Country manažer skupiny AGC Miloslav Zoula.
To je v Česku na úplném začátku, řeší se prozatím pouze na univerzitní půdě. Zachytávání, zpracování a ukládání uhlíku otevřelo letos částečně cestu ministerstvo životního prostředí, když v polovině března vláda schválila příslušný akční plán.
Společnost AGC Glass Europe má cíl uhlíkové neutrality nastavený na rok 2050 a v současné době zpracovává strategii pro jednotlivé evropské závody. „Prvním krokem v konkrétním plánu je do roku 2030 snížení celkové produkce emisí oxidu uhličitého o 30 procent pro Scope 1 a 2. Referenčním rokem je 2019,“ podotýká Miloslav Zoula.
Sny o vodíku
Klíčovým nástrojem k dekarbonizaci sklářství bude částečná elektrifikace výroby. Odklon od zemního plynu je ale komplikovaný, zejména kvůli kvalitě vyrobeného skla a možnosti dosáhnout potřebné teploty. Čím kvalitnější sklo, tím je energeticky náročnější. Navíc je nutné zajistit dostatek zelené energie.
Celoelektrické pece jsou denně schopné tavit pouze menší množství materiálu, takže se ve velkých výrobách použít nedají. Výhodnějším řešením mohou být hybridní pece kombinující elektřinu s dalšími palivy jako ta, která funguje v Barevce.
Využít by se dal ke spalování také vodík. K tomu však v současné době v Česku chybí potřebná distribuční síť, nepostačuje ani jeho výroba. Budování nových technologií přitom bude pro firmy finančně i kapacitně náročné. Pomoci jim mohou dotace z Modernizačního fondu.
Ke snížení emisí může přispět i zmíněné zvýšení recyklované složky. Ta se totiž taví při nižší teplotě. Dalšími kroky může být konkrétní úprava podmínek při tavení, jako je zvýšení poměru kyslíku nebo digitální řízení celého procesu.
Elektřinu a vodík doporučuje také velká srovnávací studie různých přístupů k dekarbonizaci výroby skla z roku 2021, která vyšla ve vědeckém časopise Energy conversion and management: X. Její autoři zmiňují rovněž využití odpadního tepla z výroby při tavení. Zdůrazňují ale, že se cena zeleného paliva musí snížit oproti těm fosilním.
Moser pohánějí baterky ze škodovek
Karlovarský Moser řeší energetickou náročnost výroby skla tím, že se pustil do výroby vlastní elektřiny. Minulý rok na jaře spustil fotovoltaiku s maximálním výkonem 527 kilowattů. Celkově elektrárna pokryje zhruba polovinu spotřeby firmy. Většina jde do chladicích pecí, sklářské fungují na plyn.
Více než tisícovku panelů doplňuje dvojice baterií o kapacitě 600 kilowatthodin. Tu tvoří akumulátory určené původně do elektromobilů mladoboleslavské Škody Auto. Články neprošly finální kontrolou pro provoz elektromobilů, pro akumulaci je nicméně jejich kapacita dostačující.
„Snižování energetické a emisní náročnosti sklářského průmyslu je náročný úkol a my k němu přistupujeme se vším respektem. Největší potenciál pro snížení emisí CO2 má právě náhrada fosilního zdroje pro tavení skla a zajištění dostatku bezemisní energie,“ vysvětluje mluvčí Skupiny ČEZ Roman Gazdík.
ČEZ ESCO, což je část polostátního energetického koncernu zaměřená na energeticky šetrné technologie, zákazníkům nabízí možnost vybudování vlastního zdroje s baterií, nebo uzavření dlouhodobého kontraktu na dodávku elektřiny za ujednanou cenu, takzvaného Power Purchase Agreement. „Typickým přístupem je postupná náhrada plynových zdrojů za elektrifikované tak, aby bylo možné zajištění dostatku zelené elektřiny na jejich provoz a firma i její zaměstnanci si na nové technologie postupně zvykali,“ popisuje Gazdík.
Ušetřili peníze i zdroje
Nové cesty k dekarbonizaci hledají také výrobci českého křišťálu Bomma a Rückl spojené ve skupině Bomma & Rückl Group. „Spotřebu energie a s ní i uhlíkovou stopu nelze snižovat omezením přísunu energie, ale především modernizací tavicích zařízení,“ vysvětluje Marketing Specialist společnosti Bomma Zuzana Kozlová.
Novou pec Bomma spustila v provozu sklárny v roce 2023 ve Světlé nad Sázavou. „Po více než roce můžeme potvrdit, že tato změna výrazně zvýšila efektivitu výroby a přispěla k úsporám jak finančních, tak fosilních zdrojů,“ říká Kozlová. Díky peci se podařilo snížit emise o 800 tun ekvivalentu CO₂ ročně, koupi podpořil dotační program Úspory energie.
Sklárna Rückl ve středočeském Nižboru zase plánuje spustit elektricky otápěnou pánvovou pec během tohoto měsíce. Měla by výrazně snížit spotřebu energie i vypouštěné emise.
Postupně ale obě sklárny zavádějí i další kroky. „V obou našich provozech využíváme odpadní teplo z tavení, například k vytápění společných a kancelářských prostor. Zároveň zpracováváme odpadní střepy z naší produkce, které přetavujeme do nových skleněných originálů,“ dodává Kozlová.
Recyklovaný materiál jsou schopni zpracovat ze sta procent, ať už ho znova nataví nebo použijí na nový materiál Fragmentglass, který vyvinuli ve spolupráci s designéry ze Studia DECHEM.
V Kyjově připravují fotovoltaiku
Ve výrobě obalového skla hraje zásadní roli recyklace už dnes. Společnost Vetropack Moravia Glass vyrábí v Kyjově nové skleněné obaly ze směsi, kterou až ze tří čtvrtin tvoří střepy. Podíl by chtěli ještě zvýšit, ale k tomu nemají dostatek použitého skla. Firma aktuálně hledá další cesty, jak výrobu zefektivnit.
Za nejperspektivnější technologii pro toto odvětví považuje Communications Specialist firmy Regína Bělohoubková zvýšení podílu elektrických tavicích agregátů poháněných obnovitelnými zdroji. V rakouském závodě už mají vlastní fotovoltaiku, v Kyjově je projekt zatím ve fázi příprav.
Do roku 2030 chce Vetropack snížit emise CO₂ ve Scope 1 a 2 o 50,4 procenta a ve Scope 3 o 30 procent. Pomáhá mu v tom firemní dekarbonizační mapa a zapojení do Science Based Targets initiative. Na vývoji navíc spolupracuje s evropskými partnery a s vlastním inovačním centrem.